More Than Just Nails and Glue: The Alchemy of Wood
The scent of freshly cut wood, the grain rising like ancient maps beneath your fingertips… for those of us drawn to the craft of building model ships, it’s a sensory journey far beyond mere construction. It's an act of connection – to history, to artistry, and to the very soul of the material we shape. While the final product – a miniature replica of a majestic clipper, a formidable warship, or a graceful merchant vessel – is undeniably beautiful, the true magic lies in the process, in the subtle alchemy of transforming raw wood into intricate, enduring components. It’s more than just nails and glue; it’s understanding the whispers of the wood itself.
My own fascination began, not with a ship, but with an old accordion. My grandfather, a taciturn man of few words, possessed one, a battered instrument salvaged from a pawn shop. The bellows were cracked, the keys stubbornly silent, but the wood… the wood was exquisite. Cherry, I later learned, with a warmth and depth of color that defied description. He’s explained, haltingly, that it was the wood's resilience, its capacity to withstand constant flexing, that impressed him. That lesson—the inherent strength *and* fragility within a natural material—stuck with me. It's the same principle at play when building a model ship.
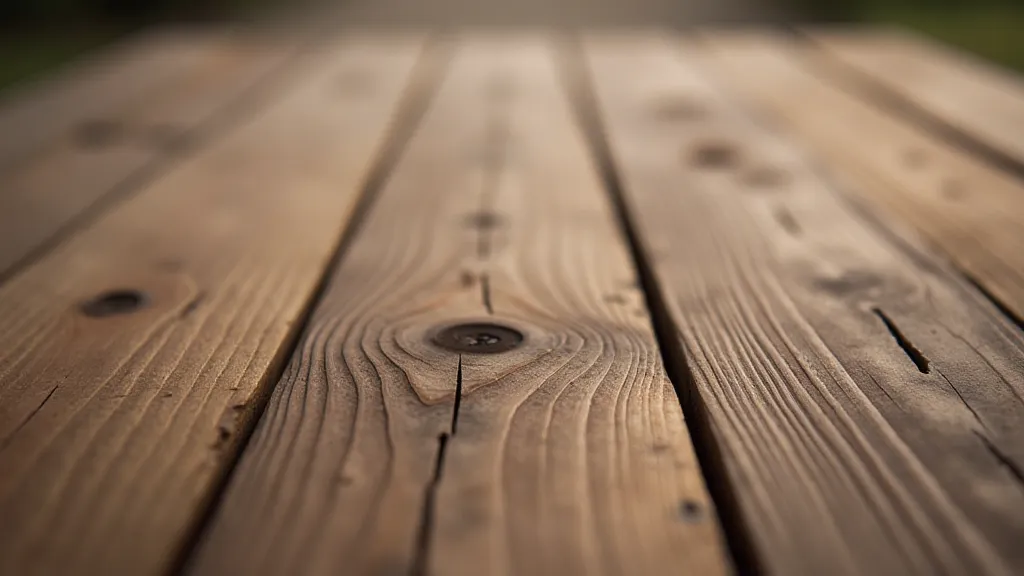
The Wood's Story: Choice and Character
The selection of wood is the first, and perhaps most crucial, step. We’re not simply grabbing any piece of lumber; we’re choosing materials imbued with specific qualities that will dictate the ship’s appearance, strength, and longevity. Mahogany, with its rich reddish-brown hue and workability, remains a classic choice for hulls and decks. Oak, historically prized for its durability and resistance to rot, is often used for framing and structural elements. Pine, softer and easier to carve, finds its place in smaller details and less critical areas. Each species tells a story – of climate, of growth, of the trees’ life cycle.
Consider the concept of “figure.” This refers to the unique patterns and irregularities within the wood’s grain. A piece of mahogany displaying “curly” figure, with its rippling, almost wave-like appearance, is significantly more valuable than a piece with straight, uniform grain. This figure isn’t just aesthetic; it affects the wood's bending properties and its response to finishes. Understanding these subtleties is a mark of a true craftsman.
The Chemistry of Adhesion: More Than Just Glue
The act of joining wood pieces is far more complex than simply applying glue and clamping. While modern adhesives offer impressive bonding capabilities, understanding the underlying chemistry is vital for achieving lasting strength. Traditional shipbuilders relied heavily on hide glue – a naturally derived adhesive made from animal collagen. This glue possesses remarkable properties – it's relatively strong, reversible (important for repairs), and doesn't chemically attack the wood.
Modern alternatives, like aliphatic resin and polyurethane glues, offer different advantages, such as increased water resistance and faster setting times. However, they also introduce different considerations. Aliphatic resin glues, for example, tend to remain somewhat flexible, which can be beneficial for joints that experience stress. The key is to choose the right adhesive for the specific application, considering factors like wood species, joint design, and anticipated environmental conditions.
Shaping and Sculpting: The Art of the Plane and File
Once the wood is chosen and the joints prepared, the shaping process begins. This is where the true artistry shines through. Traditional ship modelers relied heavily on hand tools: planes, files, chisels, and rasps. These tools, honed to razor sharpness, allow for precise control and a level of detail that’s difficult to achieve with power tools. The feel of the wood grain beneath the blade, the subtle give and resistance – it's a conversation between the craftsman and the material.
The process isn’t simply about removing wood; it's about revealing the form that’s already latent within. A skilled modeler can coax delicate curves and intricate details from a block of wood, guided by their understanding of the ship’s original design and the wood’s inherent properties. Each shaving, each file stroke, brings the model closer to life.
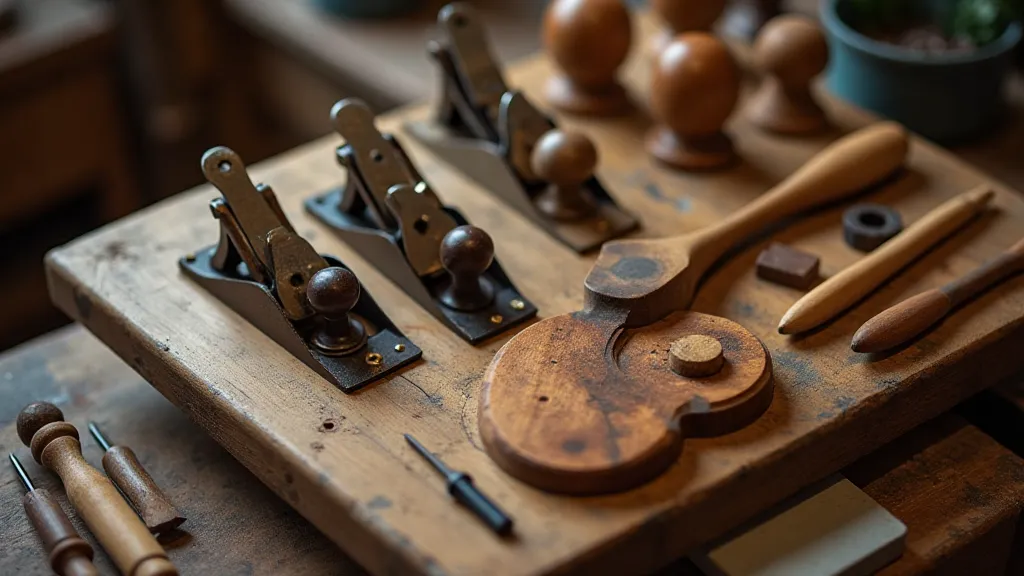
Finishing Touches: Protecting and Enhancing the Beauty
The finishing process isn't just about aesthetics; it’s about protecting the wood from moisture, UV damage, and wear. Traditional finishes often involved multiple coats of varnish or shellac, applied with meticulous care. These finishes not only enhanced the wood’s natural beauty but also created a durable barrier against the elements.
Modern finishes, such as polyurethane and acrylic lacquers, offer improved durability and ease of application. However, it’s important to choose a finish that’s compatible with the wood species and that won’t obscure the natural grain. A poorly applied finish can detract from the model’s appearance and even damage the wood itself.
A Legacy of Craftsmanship: Connecting to the Past
Building model ships is more than just a hobby; it's a connection to a rich heritage of craftsmanship and maritime history. It's a way to appreciate the skill and ingenuity of the shipbuilders who created these magnificent vessels, and to preserve a piece of that history for future generations. Each model we build is a testament to the enduring power of human creativity and the beauty of the natural world.
My grandfather rarely spoke of his accordion, but I think he understood that its value wasn't merely monetary. It was the memory of the craftsman who built it, the echoes of the music it once produced, and the tangible link to a bygone era. Building model ships gives me a similar feeling – a profound sense of connection to the past and a deep appreciation for the artistry of those who came before us. It’s a journey of discovery, a meditative process, and a way to honor the legacy of the master shipwrights who shaped our world. And it all starts with understanding the alchemy of the wood itself.
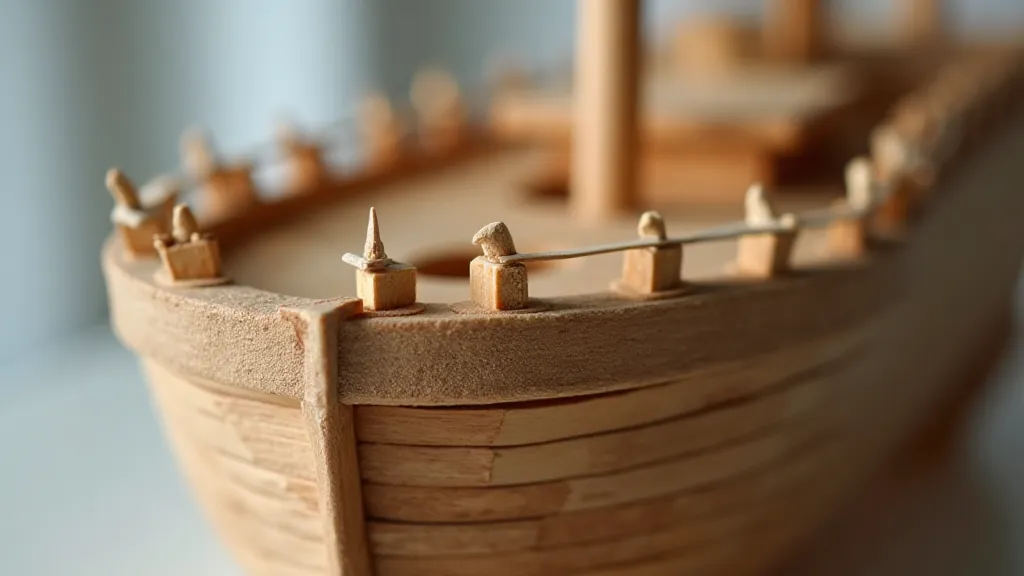